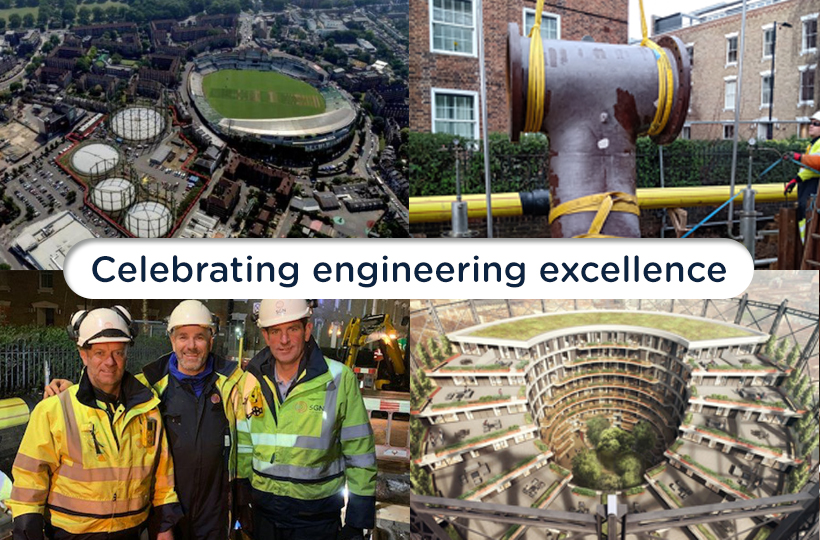
Matt Dongworth from our Southern Maintenance Transmission project team shares his experience on helping to transform an iconic landmark
You might associate the Oval with its rich history of cricket matches. For us at SGN, it’s also home to iconic Gasholder No. 1.
Built in 1847, it was the largest gas holder in the world!
However, since the modernisation of our gas networks, gas holders have been disused for a long time, with many sites going on to be redeveloped for housing, commercial properties and as areas of nature. Our Oval site is no different and it’s now being redeveloped from a local engineering depot and gas holders into a plot of land, ready for new owners to build a state-of-the-art development. This includes 1,250 new homes, recreational areas, office spaces and 1,400 jobs.
For us, this has meant relocating the gas infrastructure that supplies the site – which has involved one of the most challenging mains diversion projects ever.
Through planning, design and construction, diverting these mains posed numerous engineering obstacles.
Pipeline pressures
Our first was the proposal to use two lengths of our largest diameter pipe, 630mm polyethylene (PE), but detailed network analysis found a pressure drop would not meet local gas demand. So, for the first time on our network, we trialled installing a single 800mm PE pipe and developed a flow stopping policy for this size main which we shared with other networks.
When it came to connecting the pipe to the existing main, we faced another challenge – there wasn’t enough room in the road for a traditional Drilling RIG in the utility congested roads.
Trial holes proved there was a route in the road somewhere between the electricity cables, telephone and fibre optic cables, water mains, gas mains and a 6m diameter Victorian sewer chamber. We negotiated a one-way system with Lambeth council while also holding back traffic during times where both lanes were needed for loading and clearing materials.
Our engineers found a way to lay almost 50m of 800mm PE pipeline from the former depot’s main entrance, along Kennington Oval and ending at Vauxhall Street, ready for a tricky connection to an existing 30” cast iron low pressure (LP) main.
Tee time
The Vauxhall Street end of the project posed further challenges. A 30” tee in the original design was found to have the potential to reduce pressures required at particular levels of demand.
We needed to install a 30” equal tee, which was a bespoke fabrication carried out by Flow-stop Services.
We were able to fabricate a tee that included a subtle bend in the outlet connection to help it manoeuvre through the multiple utilities exposed in the connection excavation.
After a couple of hours of careful manoeuvring, our team were able to get the 1.5 ton 30” tee bolted into position, a valve installed and ready for the tricky connection piece from the laid 800mm PE.
Outside the original gas holder site gate, we had an intermediate pressure (IP) inlet feeding our new gas governor. However, we faced a very challenging engineering obstacle – our Drilling RIG was longer than the space available and obstructed by multiple utilities at the same ground level.
We could have drilled from the other side and used a convoluted system of bends to get back to the left-hand side. However, this would have involved significant excavations to enable the installation of the Drilling RIG, as well as needing to dismantle boundary wall of the Oval Cricket ground.
To overcome the problem, our team looked outside the industry, and the country, for the answer.
In a world-first for our industry, we developed the use of a Spherical Tee. Adopted from the American oil industry, this innovative vertical drilling technique reduced the size of the required excavation by 240m³.
These engineering and technical challenges were identified at the planning stage, which meant we were ready for them.
We’ve kept the region up to speed to ensure they’re prepared for any eventuality regarding the 800mm pipe. It’s a very enjoyable and challenging project and wouldn’t be possible without collaborative working with Lambeth Council, Cadent, Phoenix Civils, Flow-Stop Services and a number of our colleagues across different departments.
Our pioneering team has engineered a solution that not only enabled us to complete an otherwise inaccessible connection, but also significantly reduced the environmental impact of our activity. Following this successful trial, we’re now using 800mm pipe at other locations on our network.